Production > CEMENT > Technology
CEMENT PRODUCTION PROCESS
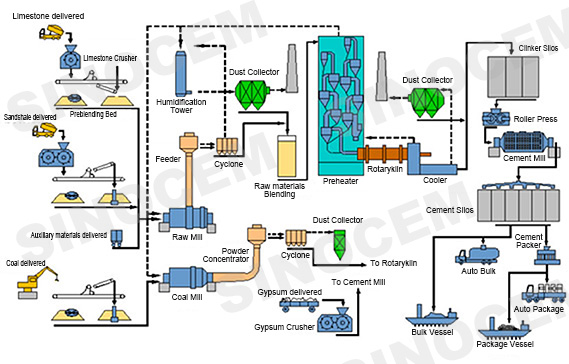
The portland cement production includes 3 main stages: raw materials preparation, clinker burning and cement milling.
1. Preparation of Raw Materials
Limestone is the main component in the production of cement. The raw materials are drilled or blasted out and delivered by trucks to the crusher, where the rock is crushed to small fragments, after which they are stored ready for use. Next, the raw materials are combined in the corrects amounts, and fed into the raw mill, where they are grounded, mixed and introduced into the rotary kiln in a dry state.
2. Clinker Burning
Our Technical Advantages:
Vertical mill: Using vertical mill technology in Raw Milling stage, which provides good fineness and high
efficiency, to produce higher quality cement. Other advantages of vertical mill are: small size, rollers wastage rate is low, saving anergy and saving production cost.Pre-heating: In the rotary kiln, the first process is pre-heating. The combined materials are fed through a series of vertical cyclones. As the material moves through these cyclones, it comes into contact with the hot kiln exhaust gases pre-heat the material before entering the main part of the kiln.
Decomposition: The pre-heat process allows the chemical reactions that take place in the kiln to happen quicker and more efficiently, to compete decompostion.
Burning: In the main kiln, the raw materials are heated to approximately 1450℃, the initial raw ingredients combine to form clinker.
Cooler: After burning, clinker is cooled in the clinker coolers before being stored in the clinker silo and ready to use.
Our Technical Advantages:
Waste Heat Recovery (W.H.R) Technology: China has become the leader in applying WHR technology in cement industry. Chinese cement capacity represents 60% of World capacity, and 95% cement plants in China has already installed W.H.R system. The principle of WHR is to recover the waste heat released from the clinker cooler and the kiln preheater system, then converted into power through a turbo-generator.
Applying WHR to a 5000tpd clinker line can produce 21,000-24,000kWh every day by itself, provide up to 30% of a cement plant’s overall electricity needs, saving 250,000 tons of coal and reducing 60,000 tons of CO2 every year.Clinker, gypsum, and mixing materials after proportioning from the proportion station, shall be fed into the roller press at the cement ball mill system. The material after grinding, shall go into the cement mill, producing cement. The finished cement is stored in cement silos, or delivered to the packing station for package cement.
Our Technical Advantages:
Ball Mill System:Using Ball Mill technology in Cement Milling stage. Cement after milling in ball mill system is in good fineness, grain shape is closed to spheroidal, which helps for hydration reaction much better than platy cement from vertical mill. Ball milling cement has high early strength, requiring less water, good mix ability that helps for concrete not easy to be cracked. This technology is chosen to produce high quality cement.
Mature technology and stable operation.
Grinding steel balls are cheap.
Mixing Materials:
Gypsum: Adding gypsum in cement can help to retard setting time, be conducive to concrete mixing, delivery and construction. In order to advoid fast setting, about 2.5%-5% gypsum should be added into cement.
Slag: Adding slag could help to enhance cement quality: 1) Improving strength, for example: Strength 42.5 Mpa cement after adding slag could be increased up to 60 Mpa; 2) Reduce hydration heat, which helps to prevent large area of concrete not to be easily cracked; 3) Slag cement has sulfate-corrosion
resistance, carbonation resistance and alkali-aggregate reaction resistance; 4) Concrete contains slag powder, having stronger plasticity, less bleeding, and better worability; 5) Producing more ettringite crystals; 6) Enhancing harden durability, wear-resisting and efficiency of concrete.
Flyash: Cement contains flyash, having compact structure, inner surface area is smaller, water absorption is weak, requiring less of water, prevent cement from dry-shrinkage and cracking. Flyash Cement also has low hydration heat and strong corrosion resistance.